Introduction
Manufacturers who produce complex parts share a similar dilemma when it comes to balancing high production outputs, quality control and cost-effective production. All three factors are critical for success, but sometimes they seem to pull against each other. For instance, increasing production volumes can drive up the risks of defects and the resultant degraded yields can drive down output while driving up costs.
A variety of production techniques can be deployed to create complex metal parts, but each one comes with tradeoffs between the above goals. Oftentimes, the best approach is to combine multiple production methods in a manner that leverages the strengths of each one, while minimizing the weaknesses.
One very successful approach is the combination of cold forging and progressive metal stamping.
In this article, we take a look at how the resultant multi-technology approach of cold forging progressive stamping can help manufacturers produce complex metal parts in high production volumes without compromising on either quality or costs.
What is Progressive Stamping?
Progressive metal stamping is a manufacturing process whereby metal parts are created using multiple metalworking procedures applied through a series of progressive steps. This is accomplished through an automated feeding system that moves the metal raw material through each step— with one feature being created or added each time— until the final product is completed.
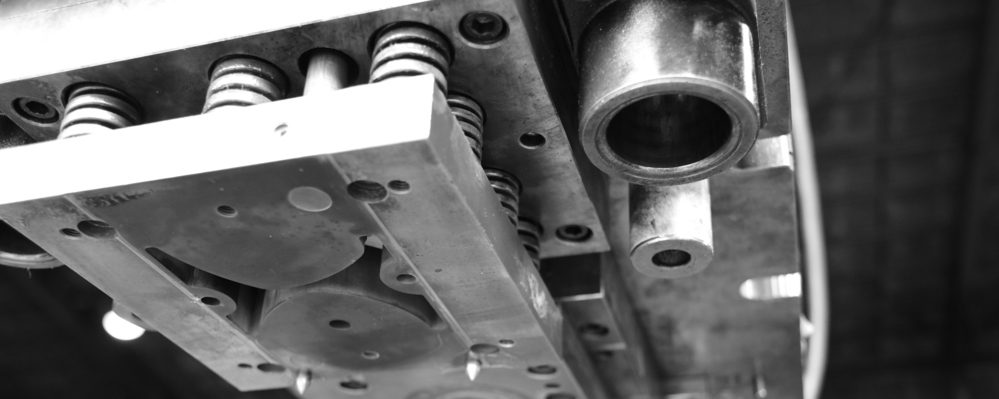
The various metalworking processes within progressive stamping can include the following:
- Extrusion: Creating the part’s desired shape by forcing the metal raw material under pressure through a die or mold
- Punching: Using a press and a punch tool to create holes in a workpiece by shearing force
- Bending: Producing V or U shapes in sheet metal and other ductile materials
- Coining: Applying force on a metal surface to achieve a smoother surface and close critical tolerance
- Deep Drawing: Forming sheet metal by using a punch to draw the metal radially into a die
- Fine Blanking: A specialty type of progressive stamping that creates flatness and full-sheared edges which cannot be accomplished through regular punching or metal cutting procedures
- Multi-slide Stamping and Four-slide Stamping: High-volume production of close-tolerance parts by use of special machinery
- Wire Forming: A complex procedure that employs forming, fabricating, assembly and finishing operations for the production of wires of various gauges
Benefits of Progressive Metal Stamping
Progressive stamping offers a number of benefits to the manufacturer and end customer, such as:
- It is a good alternative to conventional manufacturing methods by eliminating or minimizing machining, welding and assembly
- It is a stable and consistent process for the production of complex parts and products
- As raw materials are continuously being fed into the stamping machine, more parts are produced within a shorter period of time compared to conventional machining or fabrication methods
- It enables the production of parts with strong rigidity due to close tolerances, flatter and smoother surfaces, and sharper corner edges
- It can create more complex geometries in a single process
- Setup is simpler, as only one progressive machine is required to handle several manufacturing operations
- With just a single progressive metal stamping taking place, the output yield is higher, but cost per part is much lower
- It allows high repeatability with reduced risks of deformation, degradation, and other defects that accompany long production runs
- It reduces manufacturing lead time and improves overall production efficiency
What is Cold Forging?
Cold forging is an impact forming process that deforms a piece of raw material plastically, under high compressive force, between a punch and a die using suitable equipment such as a machine press.
Cold forging techniques include extrusion (forward, backward, forward and backward), coining, upsetting, and swaging. These techniques may take place in the same punch stroke or in separate operations, depending on the specific application requirements.
In essence, cold forging is a displacement process that forms existing material into the desired shape— in contrast to conventional machining, which removes material to create the desired shape.
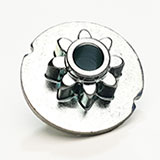
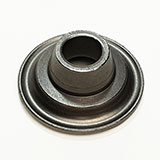
Benefits of Cold Forging
- Increased productivity for high-volume production: Cold forging is typically a single-pass forming process that deforms the existing material into the desired shape
- Time savings per part: Depending on the specific part parameters, the time savings per piece can deliver major productivity advantages; some parts that take 3 to 5 minutes per piece to be machined have seen throughput of over 50 parts per minute when successfully converted to cold forging
- Excellent Return on Investment (ROI): The opportunity for achieving over 100 to 200 times productivity improvement offers fast ROI on the investments in cold forging die and tooling
- Elimination of waste: Input to the cold forging process is in the form of “billets” of material, which are cut from the raw stock bulk material (coil, beam, sheet, etc.), with each billet being the exact amount of material needed for the final part
- Material savings and cost reduction: Instead of removing a significant amount of the raw material, a cold forging process makes use of it all— hence eliminating wasted material
- Improved part integrity and strength: The high compression process used in cold forging displaces and rearranges the grain of the base material— consequently, any inherent weaknesses are eliminated, yielding stronger parts
- Enhanced appearance and surface finishing: Cold forging also offers distinct advantages over machining, casting, weldments and other fabrication processes in that the part appearance and surface smoothness does not typically require post-processing steps
What is Cold Forging Progressive Stamping?
The combination of cold forging and progressive stamping into a complementary process can be even more powerful than using either methodology by itself. Integrating these processes helps to overcome any downsides that might result from using only one or the other.
Both cold forging and progressive stamping require large presses and dies to form parts. However, the cost, size and footprint of the machines for different processes can vary; and cost-effectiveness is highly dependent on machine utilization factors. Unless the chosen process is optimal for all of the operations needed in a complex part, it is likely that machine utilization will suffer on some operations while being excellent on others.
By combining both methodologies, cold forging progressive stamping ensures that each step in the sequence employs the most appropriate method and that machine utilization and quality output are optimized throughout the production flow.
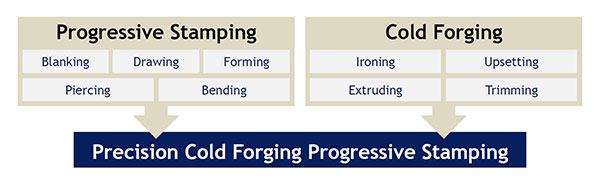
Cold forging progressive stamping offers an ideal solution for cost-effective, high-volume production of parts with multiple complex features, especially when the features need to be implemented in three-dimensional designs. The following pictures depict some examples of finished precision cold forging progressive stamped parts:
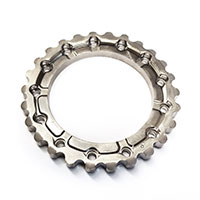
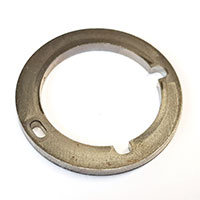
Casing Ring
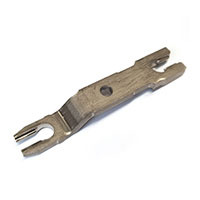
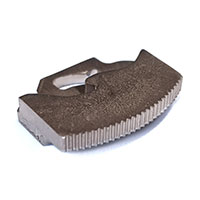
Benefits of Cold Forging Progressive Stamping
Cold forging progressive stamping is an alternative to conventional manufacturing methods; some of its key benefits include:
- Significant cost savings
- Stable precision parts
- Parts that are more rigid with close tolerances, sharper corner edges, and better flatness
- Shorter manufacturing lead-time
- Enhanced quality
- Capability for process conversion
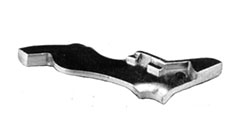
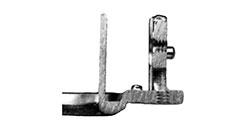
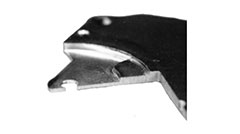
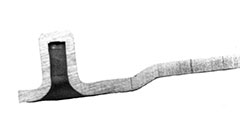
Up to 3x Material Thickness
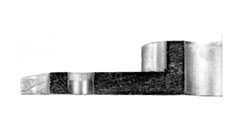
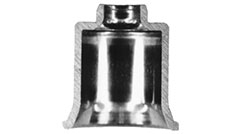
Applications of Cold Forging Progressive Stamping
Cold forging progressive stamping can be used to cost-effectively produce high volumes of complex parts across a variety of industries, including but not limited to:
- Automotive
- Medical and life sciences
- Electronics
- Aerospace
- Military defense
- Home appliances
- Architectural components
- Processing equipment
- Musical instruments
- Food and beverage
Summary
With cold forging progressive stamping, manufacturers can enjoy the harmonious interaction between efficiency, quality and overall cost. Product quality need not suffer due to higher defect rates in high-volume production runs and production costs are not hampered by sub-optimal machine utilization.